What is Porosity in Welding: Key Elements and Their Effect On Weld Top Quality
The Scientific Research Behind Porosity: A Comprehensive Guide for Welders and Fabricators
Comprehending the complex systems behind porosity in welding is vital for welders and makers pursuing remarkable craftsmanship. As metalworkers explore the midsts of this sensation, they reveal a globe regulated by numerous variables that affect the development of these tiny spaces within welds. From the structure of the base materials to the details of the welding procedure itself, a wide variety of variables conspire to either worsen or ease the existence of porosity. In this detailed guide, we will decipher the science behind porosity, discovering its results on weld high quality and unveiling advanced strategies for its control. Join us on this trip via the microcosm of welding flaws, where precision fulfills understanding in the search of flawless welds.
Understanding Porosity in Welding
FIRST SENTENCE:
Exam of porosity in welding reveals important understandings into the honesty and top quality of the weld joint. Porosity, characterized by the existence of dental caries or voids within the weld steel, is a common issue in welding processes. These gaps, if not effectively addressed, can endanger the architectural stability and mechanical residential properties of the weld, leading to possible failings in the ended up item.
To spot and measure porosity, non-destructive screening methods such as ultrasonic testing or X-ray assessment are usually utilized. These strategies permit the identification of inner flaws without jeopardizing the integrity of the weld. By assessing the size, form, and circulation of porosity within a weld, welders can make informed choices to boost their welding processes and achieve sounder weld joints.
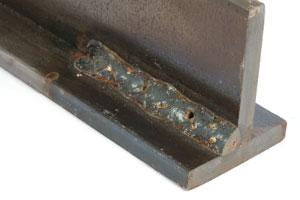
Variables Influencing Porosity Development
The occurrence of porosity in welding is affected by a myriad of variables, varying from gas protecting performance to the details of welding criterion setups. One crucial variable adding to porosity formation is poor gas protecting. When the securing gas, usually argon or carbon dioxide, is not properly covering the weld swimming pool, climatic gases like oxygen and nitrogen can contaminate the molten metal, resulting in porosity. Furthermore, the cleanliness of the base products plays a significant duty. Impurities such as rust, oil, or moisture can evaporate during welding, creating gas pockets within the weld. Welding specifications, consisting of voltage, present, take a trip speed, and electrode type, likewise impact porosity development. Using inappropriate setups can create too much spatter or warm input, which subsequently can lead to porosity. The welding method utilized, such as gas steel arc welding (GMAW) or shielded steel arc welding (SMAW), can influence porosity formation due to variations in warm distribution and gas protection. Recognizing and controlling these aspects are vital for decreasing porosity in welding procedures.
Impacts of Porosity on Weld Quality
Porosity formation dramatically compromises the architectural honesty and mechanical homes of bonded joints. When porosity is existing in a weld, it creates voids or cavities within the product, decreasing the total toughness of the joint. These spaces act as anxiety focus points, making the weld much more at risk to breaking and failing under load. The existence of porosity additionally compromises the weld's resistance to corrosion, as the entraped air or gases within the spaces can respond with the surrounding setting, leading to deterioration in time. In addition, porosity can you can try here prevent the weld's capability to stand up to stress or effect, more jeopardizing the overall quality and reliability of the bonded structure. In important applications such as aerospace, vehicle, or architectural constructions, where safety and security and longevity are extremely important, the destructive impacts of porosity on weld high quality can have serious effects, emphasizing the relevance of decreasing porosity with appropriate welding techniques and treatments.
Strategies to Lessen Porosity
Additionally, using the suitable welding specifications, such as the proper voltage, existing, and take a trip speed, is vital in preventing porosity. Maintaining a regular arc size and angle throughout welding additionally aids lower the possibility of porosity.

In addition, choosing the appropriate protecting gas and maintaining appropriate gas circulation rates are vital in decreasing porosity. Using the proper welding strategy, such as back-stepping or using a weaving activity, can additionally help disperse heat uniformly and minimize the chances of porosity formation. Ensuring correct air flow in the welding atmosphere to eliminate any possible resources of contamination see this is vital for attaining porosity-free welds. By implementing these techniques, welders can properly lessen porosity and generate high-grade welded joints.

Advanced Solutions for Porosity Control
Carrying out innovative technologies and ingenious methods plays an essential role in accomplishing exceptional control over porosity in welding processes. One innovative option is the usage of sophisticated gas combinations. Securing gases like helium or a mixture of argon and hydrogen can help in reducing porosity by giving better arc stability and boosted gas coverage. In addition, employing advanced welding methods such as pulsed MIG welding or customized environment welding can likewise aid minimize porosity issues.
One more sophisticated solution includes the usage of innovative welding devices. For example, using devices with built-in attributes like waveform control and innovative source of power can enhance weld top quality and lower porosity dangers. The application of automated welding systems with exact control over specifications can substantially lessen porosity defects.
Moreover, including advanced monitoring and examination modern technologies such as real-time X-ray imaging or automated ultrasonic screening can assist in identifying porosity early in the welding procedure, permitting for immediate restorative activities. In general, incorporating these advanced solutions can considerably improve porosity control and enhance the general top quality of welded parts.
Final Thought
In conclusion, understanding the scientific research behind porosity in welding is necessary for welders and fabricators to produce top quality welds - What is Porosity. Advanced solutions for porosity control can even more go to this web-site enhance the welding process and ensure a strong and dependable weld.